La CFAO s’est progressivement développée ces dix dernières années en prothèse amovible pour la réalisation de châssis métalliques (1-5). En 2006, les premiers logiciels de CAO ont été ouverts, ce qui a permis d’exporter librement le fichier du modèle scanné. Dans cette dynamique, un prothésiste – David Négrel – a adapté un logiciel issu de l’industrie à la CFAO dentaire sous le nom Digistell (6). Ce dernier permet de modéliser à l’écran un châssis sur un modèle de travail numérisé. Le logiciel est relié à une machine-outil (imprimante 3D, machine à usiner…) qui fabrique une maquette du châssis en un matériau calcinable. Elle sera ensuite traitée selon une méthode de cire perdue conventionnelle pour obtenir le châssis métallique. Les étapes cliniques ne sont pas modifiées par la CFAO en prothèse partielle amovible métallique, le plan de traitement reste le même et la numérisation se fait à partir du maître-modèle, issu d’une empreinte secondaire (7-12). C’est à ce stade que la CFAO se distingue d’une méthode conventionnelle. Elle nécessite un scanner, un ordinateur sur lequel est installé un logiciel de modélisation et une machineoutil. La finition du châssis est réalisée manuellement, de façon classique.
1. La Station de travail de CFAO
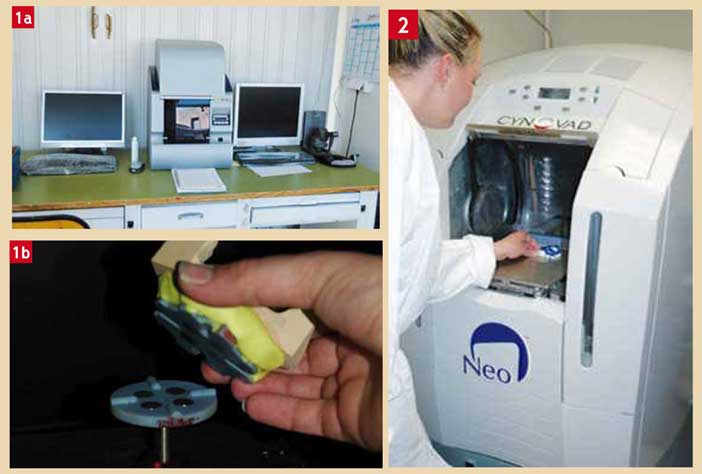
Fig. 1 : Station de travail. Les outils de CAO comprennent un ordinateur, un scanner (modèle Activity 101 fabriqué par Smartoptics), et la spatule numérique pour la V1 de Digistell (a). Une fois stabilisé sur la plaquette de transfert, le modèle, est positionné sur la rotule de la chambre du scanner (b). Fig. 2 : Imprimante 3D (modèle InVision® HR, de chez 3D® SYSTEMS, distribuée sous le nom NEO™ par la société CYNOVAD) Cette machine-outil imprime les maquettes sur leur support. Elles sont récupérées le lendemain matin lorsque l’impression est lancée le soir.
Les outils présentés ici sont un exemple d’assemblage exploité dans un laboratoire de prothèse à Strasbourg (13, 14). Les combinaisons avec du matériel d’autres fabricants sont également possibles.
a. Le scanner optique possède un compartiment (chambre de scannage) dans lequel le maître modèle est inséré pour sa numérisation. Une rotule, placée au milieu de la chambre, permet de recevoir le modèle monté sur une plaquette servant de support (Fig. 1a et b). b. L’ordinateur n’est généralement dédié qu’à la chaîne d’exploitation de CFAO : les logiciels de commande du scanner, de CAO et de FAO sont installés dessus (Fig. 1a). Racheté et exploité par une société française (C4W©), Digistell existe actuellement sous une autre version plus intuitive (Digistell V2) (15). Le châssis modélisé grâce au logiciel de CAO est enregistré au format informatique STL, puis il est exporté vers un logiciel de FAO (Invision™ de 3D Systems®). Un espace de travail – le plateau d’impression – permet de positionner ce châssis virtuel que la machine de FAO va transformer en maquette calcinable. c. La spatule numérique est un bras à retour de force qui remplace une souris d’ordinateur pour la modélisation du châssis (Fig. 1a). Cet outil retransmet des sensations au prothésiste comme s’il manipulait un modèle réel. Il peut percevoir les différents reliefs du modèle, les textures etc., ce qui apporte un réel avantage, mais le temps d’apprentissage est long. La deuxième version de Digistell ne permet plus d’utiliser cette spatule numérique en la remplaçant par une souris. d. La machine-outil de FAO Les principaux procédés actuellement utilisé sont l’impression 3D et l’usinage de matériau calcinable. En effet, l’usinage direct de métal à base de chrome cobalt est encore trop complexe et trop onéreux.
Le fait d’obtenir une maquette et non un produit fini constitue le prototypage rapide. Les châssis métalliques présentés dans cet article sont réalisés grâce à une imprimante 3D (Fig. 2), commandée depuis son pilote d’impression installé sur l’ordinateur (Invision de 3D® Systems). Cette machine possède deux têtes d‘impression : l’une pour la cire de support blanche et l’autre pour la résine acrylique calcinable bleue. Ces deux matériaux sont apposés couche après couche pour éviter les déformations : après chaque passage des têtes, la résine est photopolymérisée et la cire refroidie. De ce fait, la réalisation d’une maquette est assez longue (8 à 10 heures). La maquette terminée fait corps et repose sur un bloc de cire blanche.
2. Etapes de réalisation d’un châssis par CFAO
La CFAO proprement dite se déroule en trois étapes successives :
- numérisation du maître-modèle a l’aide du scanner
- modélisation du châssis à l’écran sur le modèle de travail virtuel
- réalisation d’une maquette de châssis par une machine-outil, ici une imprimante 3D
Les deux premières étapes constituent la CAO, la dernière étant celle de la FAO.
Cas Clinique
Le cas clinique présenté dans cet article est un édentement mandibulaire de classe II1 de Kennedy. Les couronnes supports de crochet (37,34 et 43 et 44) possèdent une armature en zircone (16). L’empreinte secondaire est réalisée avec les couronnes stabilisées (et non scellées) sur leur moignon afin de réaliser le châssis par CFAO directement dessus (Fig. 3).
a. Numérisation du maître-modèle
Le modèle est positionné sur une pâte à modeler (clay) qui repose sur une plaquette de transfert. Dans la première version de Digistell (V1), la détermination de l’axe principal d’insertion du châssis est réalisée manuellement, à l’aide d’un paralléliseur classique. La plaquette permet de replacer le modèle dans la même position sur la rotule de la chambre du scanner. L’axe principal d’insertion peut être trouvé directement grâce au logiciel de la deuxième version de Digistell. Le scanner permet de prendre d’abord une photo numérique du modèle, sur laquelle sont délimités les rebords du modèle. La numérisation 3D peut alors être effectuée. Si des zones d’ombres apparaissent, une numérisation complémentaire est nécessaire. Lorsque l’acquisition est complète, le fichier est enregistré en STL (Fig. 3).
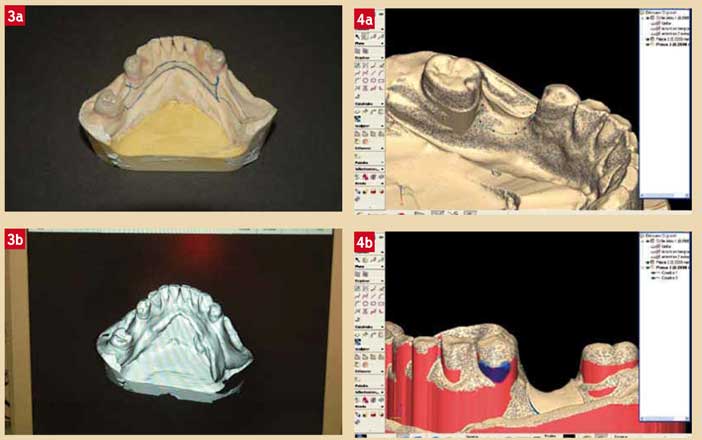
Fig. 3 : Maître-modèle Le modèle issu de l’empreinte secondaire doit être scanné (a). Si les couronnes restent sur ce modèle, il faut être vigilent à bien les stabiliser (cire). Après avoir vérifié la reproduction de tous les détails du maître-modèle, le modèle virtuel est enregistré en STL (b) Fig. 4 : Préparation du maître- modèle Les limites des selles sont tracées pour définir les zones d’espacement (a). Le modèle est mis entièrement de dépouille (en rouge) selon l’axe principal préalablement défini, et les zones de rétention des crochets sont marquées (en bleu) (b). Toutes ces modifications sont enregistrées pour créer un nouveau modèle : le modèle de travail virtuel.
b. Modélisation du châssis virtuel
Le fichier correspondant au maître-modèle est importé dans le logiciel de CAO. La première étape consiste à le transformer en modèle de travail. Le modèle est mis de dépouille dans l’axe d’insertion principal retenu avec l’articulateur. Les espacements des selles prothétiques sont tracés, gaufrés et les zones de rétention des crochets sont délimitées (Fig. 4). Ces modifications sont enregistrées, donnant lieu au modèle de travail virtuel. Ce dernier possède une consistance virtuelle qui permet au prothésiste de sentir les reliefs à l’aide de la spatule numérique. La modélisation du châssis est réalisée à partir de forme de plaque et de tube. Pour chaque élément du châssis, il faut d’abord tracer ses limites (plaque palatine, selles…) ou sa forme générale (crochets, potence…). Le logiciel leur donne ensuite une forme grossière qu’il faut retravailler à l’aide d’outils spécifiques de lissage, rognage, épaississement … (Fig. 5a). Les éléments du châssis sont conçus dans l’ordre souhaité par le prothésiste, et reliés virtuellement les uns aux autres lorsque le modelage est achevé (Fig. 5b). Des tiges de coulée sont ajoutées à cette étape avant de séparer le châssis de son support virtuel. Enfin, les selles sont extrudées toutes ensemble, selon les mêmes paramètres définis par le prothésiste (taille des trous, nombre…). La finition du modelage est nécessaire à ce stade (Fig. 5c). Le châssis finalisé est enregistré, puis exporté vers le logiciel de FAO.
c. Réalisation de la maquette calcinable
La position du châssis virtuel dans le plateau d’impression est gérée dans le logiciel de FAO. Une dizaine de châssis peut être recueillie dans cet espace (Fig. 6a). Quand le plateau est prêt, l’impression 3D peut commencer. Elle est souvent lancée le soir, pour pouvoir récupérer les maquettes le lendemain matin (Fig. 6b). La maquette doit être débarrassée de son support en cire avant la mise en cylindre. Pour cela, il est recommandé de la mettre dans une étuve bien calibrée, qui fera fondre la cire sans déformer la résine. Elle est replacée enfin sur le maître-modèle pour vérifier l’absence de déformations et son intégrité (Fig. 6c).
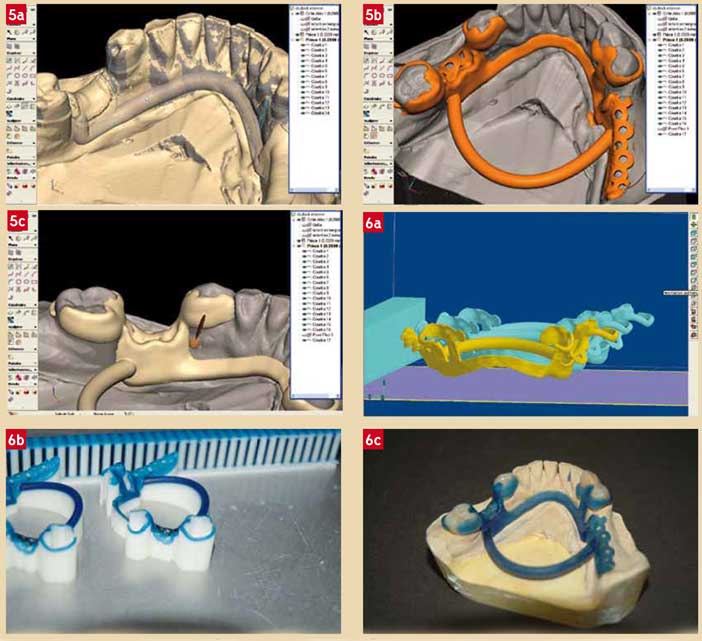
Fig. 5 : Modélisation du châssis Chacun des éléments est tracé sur le modèle de travail dans l’ordre souhaité par le prothésiste : barre linguale, crochet sur 34 (a)… Les éléments sont ensuite assemblés entre eux (b), avant de finir les zones de transition et autres imperfections (c). Fig. 6 : Réalisation de la maquette par FAO Le plateau d’impression recueille les châssis virtuel qui doivent être imprimés (a). Ils sont positionnés afin de prendre le moins de place possible. Les maquettes (en bleu) sur leur support en cire (en blanc) sont récupérées environ 8 heures plus tard dans l’imprimante (b). La maquette nettoyée est replacée sur le maître-modèle (c).
d. Coulée de la maquette
La maquette en résine est mise en cylindre directement, sans support en plâtre comme dans une technique conventionnelle (Fig. 7a). Un revêtement réfractaire adapté (à base de phosphate) est utilisé à cet effet. Jusqu’à trois maquettes peuvent être mises en place dans le même cylindre, des tiges de coulée doivent être rajoutées dans ce cas pour les réunir. Le cylindre suit une méthode de cire perdue avec des réglages classiques (mise au four et coulée du métal). L’ébarbage et le polissage sont un peu plus rapides à réaliser qu’avec une méthode conventionnelle car la maquette présente une finition déjà très satisfaisante (45 mn contre 60 mn) (Fig. 7b et c).
e. Essayage clinique
Les étapes suivantes rejoignent les étapes conventionnelles de réalisation d’une prothèse à châssis. La relation inter-maxillaires est enregistré sur le châssis, le montage des dents est essayé avant polymérisation (Fig. 8a). Enfin, le châssis est inséré et l’occlusion réglée. (Fig. 8b et c).

Fig. 7 : Coulée et finition de la maquette Les maquettes sont stabilisées sur un support avant de couler le revêtement réfractaire (a). Après la coulée et le refroidissement du métal, les châssis sont récupérés, ébarbés, séparés, polis et replacés sur leur maîtremodèle correspondant (b et c). Fig. 8 : Montage des dents et essayage clinique Le châssis est essayé en bouche avant polymérisation (a), puis est mis en place le même jour que les couronnes (b et c). Son adaptation s’avère aussi bonne qu’avec une méthode de conception classique.
Conclusion
La CFAO en prothèse amovible apporte de nombreux avantages au laboratoire de prothèse : confort de travail amélioré, économie de matériaux et précision dans la réalisation des maquettes de fonderie (13). Une erreur de coulée peut être rattrapée à partir de la réimpression de la maquette, dont le design a été enregistré. Une longue période d’apprentissage est toutefois nécessaire avant de bien maîtriser la technique (déformations de la maquette…). Ces machines ont également un coût d’acquisition et une maintenance (matérielle et informatique) à prendre en compte. De plus, cette aide technologique amène le laboratoire à s’organiser différemment dans son emploi du temps et dans la gestion des temps morts (impression 3D). En moyenne, le temps de travail nécessaire à la réalisation d’un châssis est diminué d’ 1/3 par rapport à une méthode conventionnelle. Les délais et le coût de fabrication sont donc diminués, ce qui peut avoir un impact pour le praticien. L’investissement d’un ou plusieurs laboratoires français dans cette chaîne de fabrication sera peut être une issue pour rester compétitif face au développement de la concurrence étrangère, tout en fournissant un travail de haute qualité.
Remerciements à Mme D. Trompeter, prothésiste du laboratoire Flecher (Strasbourg) pour son implication dans ce travail (photos et réalisation de la prothèse à châssis).
Bibliographie
1. Bibb RJ, Eggbeer D, Williams RJ, Woodward A. Trial fitting of a removable partial denture framework made using computer-aided design and rapid prototyping techniques. Proc Inst Mech Eng H. 2006 Oct ; 220(7) : 793-7.
2. Williams RJ, Bibb R, Eggbeer D, Collis J. Use of CAD/CAM technology to fabricate a removable partial denture framework. J Prosthet Dent. 2006 Aug ; 96(2) : 96-9.
3. Zho Nghua Kou Qiang Yi Xue Za Zhi. Computer aided design and computer aided manufacture of sacrificial pattern of removable partial denture framework. Wu L, Lü PJ, Wang Y, Ai HJ, Dong DY. 2006 Jul ; 41(7) : 432-5.
4. Eggbeer D, Bibb R, Williams R. The computer-aided design and rapid prototyping fabrication of removable partial denture frameworks. Proc Inst Mech Eng H. 2005 May ; 219(3) : 195-20.
5. Han J, Wang Y, Lü P. A preliminary report of designing removable partial denture frameworks using a specifically developed software package. Int J Prosthodont. 2010 Jul-Aug ; 23(4):370-5. 6.
6. Négrel D. Stellite par CAD-CAM : Enfin ! Technologie Dentaire. Février 2007, n°243.
7. Schittly J, Schittly E. Prothèse amovible partielle, clinique et laboratoire. Editions CdP, collection JPIO, 2006.
8. Phoenix RD, Cagna D.R., DeFreest C.F. Clinical Removable Partial Prosthodontics. Editions Quintessence books. Paris. 2003.
9. Borel J-C, Schittly J, Exbrayat J. Manuel de prothèse partielle amovible. Paris : Editions Masson, 1994.
10. Begin M. La Prothèse partielle amovible – conception et tracés des châssis. Editions Quintessence International. Décembre 2004.
11. Santoni P. Maîtriser la prothèse amovible partielle. Ed. CdP, coll. JPIO. Mars 2004.
12. Bien N. Conception et tracé des prothèses partielles amovibles. Editions Prostho. Paris. 1996.
13. Baixe S., Etienne O. Kress P., Taddei C. Apport de la CFAO en prothèse Amovible. Les cahiers de prothèse. Décembre 2010. n°152. 43-59
14. Nguyen M. Apport de la CFAO en prothèse amovible. (Thèse 3e cycle Odontol. Strasbourg. 2010. N°36). N°43.22.10.36
15. Joullie K. , Julia M., Durand J-C., Nublat C., Bertrand F., Sartorio A. Prothèse amovible partielle à infrastructure métallique : conception du châssis par CAO. Stratégie Prothétique. Jan-Fév 2011. Vol 11 (1) : 37-46
16. Etienne O., Baixe S., Magniez P., Trotzier F., Taddei C., Prothèse amovible partielle fixée à armature zircone. Association en prothèse composite. Les cahiers de prothèse. Décembre 2010. N°152. 61-70